一种振动结构、应用振动机构的液压拔管机及使
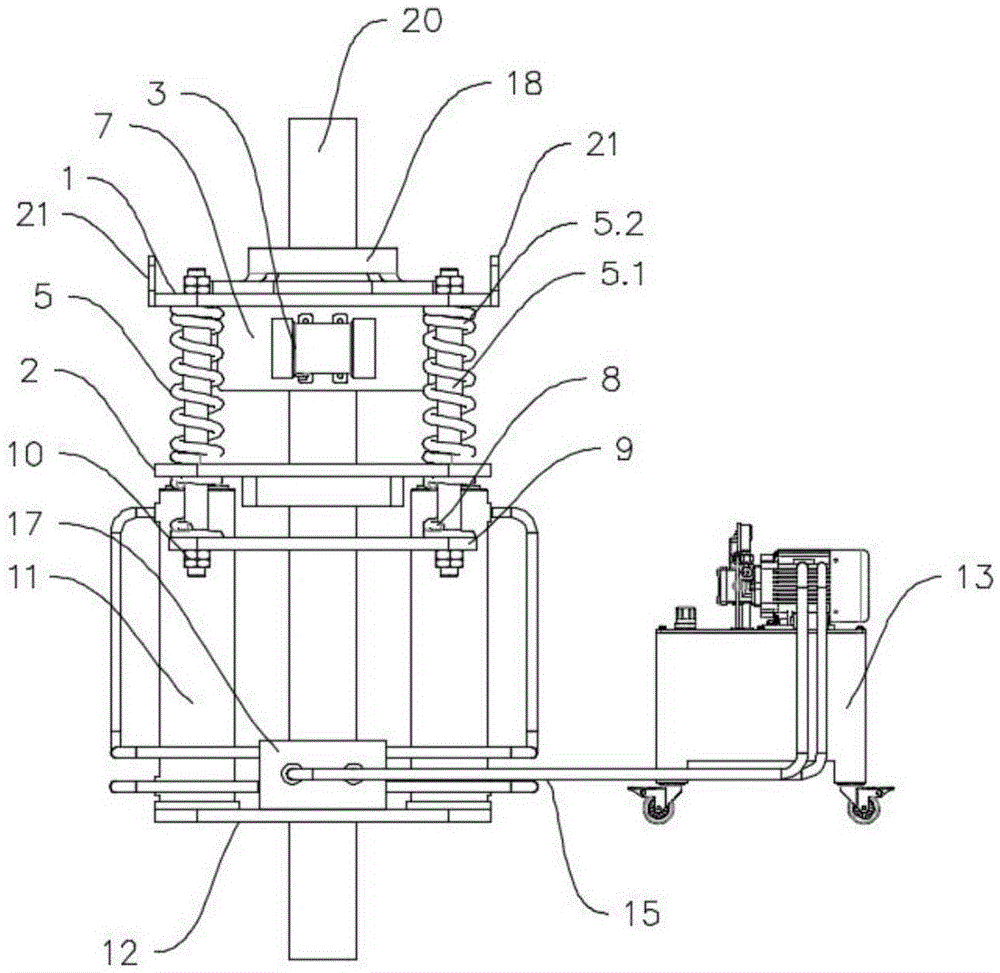
本发明属于工程机械技术领域,具体涉及一种振动结构、应用振动机构的液压拔管机及使用方法。
背景技术:
液压拔管机是各类岩土钻掘工程中钻机的配套辅助设备,适用于灌注桩、旋喷钻进、锚索孔等采用跟管钻进工艺施工的工程,用于起拔钻孔护壁套管和钻杆,也可用于各类钻具事故处理中起拔套管和钻杆。随着工程凿岩钻进技术的发展,钻孔的深度越来越深,套管跟进深度越来越大,套管起拔和回收利用的难度也越来越高。
而目前采用的液压拔管机,主要为双油缸结构,其最大起拔力一般在80t,起拔套管深度不能满足超深及复杂覆盖层钻探的需要;此外,采用传统的拔管机在起拔套管的过程中,会遇到套管被卡死的情况,对于此种情况,通常是增加起拔力,但采用此种强行拔出套管的方式会损坏套管,进一步导致不能完整的拔出套管,因此,针对上述问题,目前急需解决套管在起拔过程中被卡死而无法拔出的问题。
技术实现要素:
为了解决现有技术存在的上述现有技术中套管在起拔过程中被卡死而无法拔出的问题,本发明目的在于提供一种能够通过振动方式实现对套管的颤振,从而减小起拔力达到较好的起拔效果的新型振动式拔管机及其实现方法。
本发明所采用的技术方案为:
一种振动结构,用于振动固定在基体内的套管的装置,其中,包括用于夹紧套管的夹紧部件、设于所述夹紧部件上的振动源和与基体连接的固定机构,所述夹紧部件与所述固定机构之间设有实现夹紧部件与固定机构之间活动连接的弹性机构。
夹紧部件用于对埋于基体内的套管进行夹紧,在夹紧部件夹紧套管的状态下,通过固定机构对夹紧部件施加向上的驱动力,实现对套管的起拔,由于套管起拔的路径较深,在起拔的过程中容易出现被卡死而无法拔出的情况,因此,在夹紧部件与固定机构之间设置弹性机构,实现夹紧部件与固定机构之间的活动连接,同时通过在夹紧部件上设置振动源,在套管被卡死无法拔出的情况下,直接对套管进行振动,从而解决套管被卡死的问题,之后可以重新实施驱动力,实现对套管的拔出。
由于夹紧部件的振动直接对套管产生影响,为了减轻对固定机构的影响,因此,在夹紧部件与固定机构之间设置弹性机构,弹性机构与固定机构活动连接,弹性机构对振动具有很大程度的缓冲效果,避免振动电机的振动对固定机构产生直接的影响。
进一步的,所述夹紧部件包括顶升板,套管的上端穿过所述顶升板上所设的安装孔并通过设于顶升板上的夹紧装置实现对套管的夹紧。
进一步的,所述固定机构包括固定板,所述固定板通过所述弹性机构实现与所述夹紧部件的活动连接。
所述顶升板和所述固定板所在的平面均与套管的轴线相互垂直,套管依次穿过固定板上所设的A通孔和所述顶升板上所设的安装孔,安装孔与A通孔的轴线一致,保证在对套管进行起拔过程中,起拔力的集中,减小套管被卡死的可能。
为了实现对套管的顺利安装,A通孔与安装孔的孔径均大于套管的外径,A通孔的孔径大于套管的外径还为了减小套管颤振过程中对固定板的影响,安装孔的孔径大于套管的外径还为了实现对夹紧部件的安装。
进一步的,所述弹性机构包括至少两组均匀分布在所述顶升板和固定板之间的弹力组件,所述弹力组件包括弹簧杆和振动弹簧,所述弹簧杆的上端与所述顶升板连接,所述弹簧杆的下端穿过所述固定板上所设的A过孔,该弹簧杆伸出所述A过孔的一端连接有防止所述弹簧杆脱出的限位件,所述振动弹簧套设于所述弹簧杆上,且该振动弹簧的两端分别与所述顶升板、所述固定板相抵。
所述A过孔的孔径大于所述弹簧杆的外径并小于所述振动弹簧、所述预紧弹簧的外径,所述弹簧杆在颤振的过程中,由于A过孔的孔径较大,弹簧杆的晃动对固定板的影响较小,同时也减小了对油缸的振动,A过孔的孔径小于所述振动弹簧、所述预紧弹簧的外径能够保证振动弹簧能够与固定板的上表面相抵,预紧弹簧与固定板的下表面相抵。
弹力组件设置为两组时,则两组弹力组件对称设于A通孔的两侧,两组弹力组件的轴线与A通孔的轴线为三条轴线共面,能够保证顶升板的平衡。
值得说明的是,通过弹力组件实现对顶升板和固定板之间间距的调整,固定板与顶升板之间的间距逐渐缩小的过程中,固定板具有上驱动力的传递功能,实现对顶升板向上的驱动,具体驱动过程为:驱动杆上移过程中,带动固定板上移,固定板在上移过程中,振动弹簧逐渐压缩,固定板与顶升板之间的间距逐渐缩小,振动弹簧对顶升板具有向上的推力,可以驱动顶升板的上移。
进一步的,还包括预紧弹簧,所述预紧弹簧套设于所述弹簧杆的下端且该预紧弹簧的两端分别与所述固定板、所述限位件相抵。限位件可以直接固定在弹簧杆上,也可以套接在弹簧杆上,通过螺帽避免限位件的脱出。
值得说明的是,预紧弹簧可实现对固定板和限位件之间间距的调整,固定板和限位件之间的间距逐渐缩小的过程中,固定板具有下驱动力的传递功能,实现对顶升板的向下驱动,具体驱动过程为:振动弹簧复位后,固定板随着驱动杆的继续下移,预紧弹簧逐渐压缩,预紧弹簧对限位件的推力直接通过弹簧杆传递给顶升板,实现弹簧杆对顶升板的下拉,顶升板下移。
进一步的,所述振动源包括均匀分布的振动电机。
通过在夹紧部件上设置振动电机,振动电机对夹紧部件具有振动的效果,通过夹紧部件实现对套管的夹紧,在套管处于被夹紧状态下,振动电机的启动,能够顺利实现对套管的颤振,达到防止套管卡死,减小起拔力的目的,现有的液压拔管机在出现套管卡死,油缸无法继续顶升时,整个起拔过程便陷入僵局,无法继续实施拔管操作。本发明通过采用在夹紧部件上设置振动电机,并通过弹性机构和固定机构的配合设置,很好的解决了上述现有技术在拔管过程中遇到的问题。
本发明还提供一种采用上述振动结构的新型振动式液压拔管机,包括油缸底座和均匀设于所述油缸底座上的至少两个油缸,所述油缸的驱动杆与所述固定板固定连接。所述油缸底座上设有B通孔,所述B通孔与所述A通孔的轴线一致,所述油缸的驱动杆与所述固定板固定连接。
进一步的,所述振动电机安装在所述顶升板下部所设的抵块上,考虑到结构的稳固性,抵块与顶升板焊接成一体,抵块的作用是为了实现固定板对顶升板的直接驱动,减小力的传递过程中的损耗。考虑到固定板驱动顶升板的过程中,为了避免固定板对振动电机产生影响,所述振动电机的最下端点高于所述抵块的抵接面。
进一步的,所述夹紧装置包括卡瓦和卡瓦座。所述卡瓦座固定在所述顶升板的中部,所述卡瓦座的轴线与所述安装孔的轴线一致,所述卡瓦设于所述卡瓦座内且该卡瓦与自下向上依次穿过所述B通孔、所述A通孔、所述安装孔、所述卡瓦座的套管抱紧,所述A通孔、所述B通孔、所述安装孔、所述卡瓦座的孔径均大于所述套管的外径。
值得说明的是,本发明中的油缸为两个时,则两个油缸对称设于套管的两侧,能够保证对起拔力的平衡,避免出现起拔歪斜,套管卡死。
值得说明的是,A通孔、B通孔的孔径均大于套管的外径,套管颤振幅度能够受控制,同时由于A通孔、B通孔的孔径较大,在套管颤振过程中,对油缸底座和固定板的影响较小,一定程度上也减小了对油缸的振动。
当油缸为两个,弹力组件设置为两组时,油缸和弹力组件交叉间隔设置,即两个油缸的轴线所在的平面与两组弹力组件的轴线所在的平面相互垂直。
若油缸为三个,弹力组件为三组时,油缸和弹力组件交叉间隔设置。
若油缸为两个,弹力组件为四组时,各油缸到A通孔的距离相等,各弹力组件到A通孔的距离相等。
本发明还提供一种新型振动式液压拔管机的拔管方法,其中,包括如下步骤:
S1.安装套管,之后安装夹紧装置实现对套管上端的夹紧;
S2.启动拔管机的油缸,油缸对固定板进行驱动;
S3.固定板驱动顶升板上移,顶升板通过夹紧装置实现对套管的顶升,套管逐渐被拔出;
S4.当套管与土体之间的摩擦力大于油缸的驱动力时,油缸的驱动杆便停止上升,此时振动电机启动,通过振动电机的振动,能够实现对套管的颤振,套管在颤振的过程中,防止套管的卡死,能够一定程度的减小起拔力,振动电机启动一定时间,油缸驱动杆继续上升,再次对套管拔出,该步骤可以重复进行;
S5.驱动杆继续上升到极限位置时,通过液压换向阀控制油缸驱动杆下降,固定板随之下移过程中,固定板与抵块逐渐分离,振动弹簧逐渐复位,之后驱动杆继续下移,预紧弹簧逐渐压缩,预紧弹簧对限位件的推力直接通过弹簧杆传递给顶升板,实现弹簧杆对顶升板的下拉,弹簧杆在下拉顶升板的过程中,夹紧装置对套管的夹紧力逐渐减小,直至夹紧装置松开套管,之后夹紧装置继续下移,重新移动至起始起拔位置,重复上述操作。
本发明的有益效果为:
(1)本发明通过夹紧部件用于对埋于基体内的套管进行夹紧,在夹紧部件夹紧套管的状态下,通过固定机构对夹紧部件施加向上的驱动力,实现对套管的起拔,由于套管起拔的路径较深,在起拔的过程中容易出现被卡死而无法拔出的情况,因此,在夹紧部件与固定机构之间设置弹性机构,实现夹紧部件与固定机构之间的活动连接,同时通过在夹紧部件上设置振动源,在套管被卡死无法拔出的情况下,直接对套管进行振动,从而解决套管被卡死的问题,之后可以重新实施驱动力,实现对套管的起拔,拔管效果较之现有技术具有明显的优势,且该设计结构简单,可操作性强,易于推广使用。
(2)由于夹紧部件的振动直接对套管产生影响,为了减轻对固定机构的影响,因此,在夹紧部件与固定机构之间设置弹性机构,弹性机构与固定机构活动连接,弹性机构对振动具有很大程度的缓冲效果,避免振动电机的振动对固定机构产生直接的影响,结构设计合理,设备运行的可靠性更高。
附图说明
图1是本发明中拔管机的正视结构示意图;
图2是本发明中拔管机的后视结构示意图;
图3是本发明中拔管机的俯视结构示意图;
图4是本发明中拔管机的结构示意图;
图5是本发明中拔管机的另一视角的结构示意图;
图6是本发明中固定板的结构示意图。
图中:1-顶升板,2-固定板,2.1-驱动部,2.2-振动调节部,3-振动电机,4-A通孔,5-弹力组件,5.1-弹簧杆,5.2-振动弹簧,6-条形板,7-抵块,8-预紧弹簧,9-限位件,10-螺帽,11-油缸,12-油缸底座,13-液压站,14-B通孔,15-进油管,16-回油管,17-液压换向阀,18-卡瓦座,19-卡瓦,20-套管,21-提手。
具体实施方式
下面结合附图及具体实施例对本发明做进一步阐释。
实施例1:
本实施例提供一种振动结构,用于振动固定在基体内的套管20的装置,如图4和图5所示,包括用于夹紧套管20的夹紧部件、设于夹紧部件上的振动源和与基体连接的固定机构,夹紧部件与固定机构之间设有实现夹紧部件与固定机构之间活动连接的弹性机构。
夹紧部件用于对埋于基体内的套管20进行夹紧,在夹紧部件夹紧套管20的状态下,通过固定机构对夹紧部件施加向上的驱动力,实现对套管20的起拔,由于套管20起拔的路径较深,在起拔的过程中容易出现被卡死而无法拔出的情况,因此,在夹紧部件与固定机构之间设置弹性机构,实现夹紧部件与固定机构之间的活动连接,同时通过在夹紧部件上设置振动源,在套管20被卡死无法拔出的情况下,直接对套管20进行振动,从而解决套管20被卡死的问题,之后可以重新实施驱动力,实现对套管20的起拔。
需要说明的是,由于夹紧部件的振动直接对套管20产生影响,为了减轻对固定机构的影响,因此,在夹紧部件与固定机构之间设置弹性机构,弹性机构与固定机构活动连接,弹性机构对振动具有很大程度的缓冲效果,避免振动电机3的振动对固定机构产生直接的影响。
实施例2:
本实施例是在上述实施例1的基础上进行优化限定。
如图1-图5所示,夹紧部件包括顶升板1,套管20的上端穿过顶升板1上所设的安装孔并通过设于顶升板1上的夹紧装置实现对套管20的夹紧。
实施例3:
本实施例是在上述实施例1的基础上进行优化限定。
如图1、图2、图4和图5所示,固定机构包括固定板2,固定板2通过弹性机构实现与夹紧部件的活动连接。
顶升板1和固定板2所在的平面均与套管20的轴线相互垂直,套管20依次穿过固定板2上所设的A通孔4和顶升板1上所设的安装孔,安装孔与A通孔4的轴线一致,保证在对套管20进行起拔过程中,起拔力的集中,减小套管20被卡死的可能。
为了实现对套管20的顺利安装,A通孔4与安装孔的孔径均大于套管20的外径,A通孔4的孔径大于套管20的外径还为了减小套管20颤振过程中对固定板2的影响,安装孔的孔径大于套管20的外径还为了实现对夹紧部件的安装。
实施例4:
本实施例是在上述实施例3的基础上进行优化限定。
如图4和图5所示,弹性机构包括四组均匀分布在顶升板1和固定板2之间的弹力组件5,四组弹力组件5分别设于靠近固定板2、顶升板1的四个边角之间,弹力组件5包括弹簧杆5.1和振动弹簧5.2,弹簧杆5.1的上端与顶升板1连接,具体是采用螺帽实现对弹簧杆5.1上端的限位,弹簧杆5.1的下端穿过固定板2上所设的A过孔,该弹簧杆5.1伸出A过孔的一端连接有防止弹簧杆5.1脱出的限位件9,振动弹簧5.2套设于弹簧杆5.1上,且该振动弹簧5.2的两端分别与顶升板1、固定板2相抵,弹簧杆5.1同时垂直于顶升板1和固定板2。
A过孔的孔径大于弹簧杆5.1的外径并小于振动弹簧5.2、预紧弹簧8的外径,弹簧杆5.1在颤振的过程中,由于A过孔的孔径较大,弹簧杆5.1的晃动对固定板2的影响较小,同时也减小了对油缸11的振动,A过孔的孔径小于振动弹簧5.2、预紧弹簧8的外径能够保证振动弹簧5.2能够与固定板2的上表面相抵,预紧弹簧8与固定板2的下表面相抵。
弹力组件5设置为两组时,则两组弹力组件5对称设于A通孔4的两侧,两组弹力组件5的轴线与A通孔4的轴线为三条轴线共面,能够保证顶升板1的平衡。
值得说明的是,通过弹力组件5实现对顶升板1和固定板2之间间距的调整,固定板2与顶升板1之间的间距逐渐缩小的过程中,固定板2具有上驱动力的传递功能,实现对顶升板1向上的驱动,具体驱动过程为:驱动杆上移过程中,带动固定板2上移,固定板2在上移过程中,振动弹簧5.2逐渐压缩,固定板2与顶升板1之间的间距逐渐缩小,振动弹簧5.2对顶升板1具有向上的推力,可以驱动顶升板1的上移。
实施例5:
本实施例是在上述实施例4的基础上进行优化限定。
如图1、图2、图4和图5所示,还包括预紧弹簧8,预紧弹簧8套设于弹簧杆5.1的下端且该预紧弹簧8的两端分别与固定板2、限位件9相抵。限位件9可以直接固定在弹簧杆5.1上,也可以套接在弹簧杆5.1上,通过螺帽10避免限位件9的脱出。
具体的,位于固定板2长度方向上的两根弹簧杆5.1的下端所设的限位件9为一块共用的条形板6,条形板6的两端设有B过孔,弹簧杆5.1伸出对应的A过孔的一端套设预紧弹簧8之后再穿过B过孔,该条形板6的两端通过设于弹簧杆下端的螺帽10实现与弹簧杆5.1的连接。
值得说明的是,预紧弹簧8可实现对固定板2和限位件9之间间距的调整,固定板2和限位件9之间的间距逐渐缩小的过程中,固定板2具有下驱动力的传递功能,实现对顶升板1的向下驱动,具体驱动过程为:振动弹簧5.2复位后,固定板2随着驱动杆的继续下移,预紧弹簧8逐渐压缩,预紧弹簧8对限位件9的推力直接通过弹簧杆5.1传递给顶升板1,实现弹簧杆5.1对顶升板1的下拉,顶升板1下移。
实施例6:
本实施例是在上述实施例1的基础上进行优化限定。
如图1、图2、图4和图5所示,振动源包括均匀分布的振动电机3,通过在夹紧部件上设置振动电机3,振动电机3对夹紧部件具有振动的效果,通过夹紧部件实现对套管20的夹紧,在套管20处于被夹紧状态下,振动电机3的启动,能够顺利实现对套管20的颤振,达到防止套管20卡死,减小起拔力的目的,现有的液压拔管机在出现套管20卡死,油缸11无法继续顶升时,整个起拔过程便陷入僵局,无法继续实施拔管操作。本发明通过采用在夹紧部件上设置振动电机3,并通过弹性机构和固定机构的配合设置,很好的解决了上述现有技术在拔管过程中遇到的问题。
实施例7:
如图1-图5所示,本实施例提供一种振动结构,包括相互平行设置的顶升板1和固定板2,顶升板1与固定板2均为矩形,顶升板1和固定板2所在的平面均与套管20的轴线相互垂直,顶升板1上设有安装孔,固定板2上设有A通孔4,安装孔与A通孔4的轴线一致,顶升板1的下部设有抵块7,抵块7沿着靠近顶升板1的长度方向对称设有两块,为了达到较好的振动效果以及方便安装,振动电机3为两个且分别对称安装在抵块7的外侧壁上,考虑到固定板2驱动顶升板1的过程中,为了避免固定板2对振动电机3产生影响,振动电机3的最下端点高于抵块7的抵接面。
固定板2上设有两个驱动部2.1和四个振动调节部2.2,各驱动部2.1到A通孔4的距离相等,各振动调节部2.2到A通孔4的距离相等,即本实施例中,振动调节部2.2位于固定板2的四个边角的位置,驱动部2.1位于固定板2的两条宽度边的中部,驱动部2.1与油缸11的驱动杆固定连接,振动调节部2.2的上部设有弹力组件5,振动调节部2.2的下部设有预紧组件。
弹力组件5包括弹簧杆5.1和振动弹簧5.2,预紧组件包括预紧弹簧8和限位件9,弹簧杆5.1为四根,弹簧杆5.1的上端通过螺帽与顶升板1的四个边角处连接,弹簧杆5.1与顶升板1相互垂直,振动弹簧5.2套设在位于顶升板1和固定板2之间的弹簧杆5.1上,振动弹簧5.2的上端与顶升板1相抵,振动弹簧5.2的下端与固定板2相抵,弹簧杆5.1的下端穿过固定板2上对应位置所设的A过孔,且该弹簧杆5.1伸出A过孔的一端套设预紧弹簧8,预紧弹簧8的上端与固定板2的下表面相抵,预紧弹簧8的下端与限位件9相抵,位于固定板2长度方向上的两根弹簧杆5.1的下端所设的限位件9为一块共用的条形板6,条形板6的两端设有过孔B,弹簧杆5.1伸出A过孔的一端套设预紧弹簧8之后再穿过过孔B,该条形板6的两端通过螺帽10实现与弹簧杆5.1的连接。
条形板6通过过孔B套设于弹簧杆5.1的下端,弹簧杆5.1的下端设有限位螺帽10,条形板6的下表面与限位螺帽10相抵。
实施例8:
本实施例是在上述实施例1-7的基础上进行优化限定。
如图1、图2、图4和图5所示,本发明还提供一种采用上述振动结构的新型振动式液压拔管机,包括油缸11底座和均匀设于油缸11底座上的至少两个油缸11,油缸11的驱动杆与固定板2固定连接。油缸11底座上设有B通孔,B通孔与A通孔4的轴线一致,油缸11的驱动杆与固定板2固定连接。
实施例9:
本实施例是在上述实施例8的基础上进行优化限定。
如图1、图2、图4和图5所示,振动电机3安装在顶升板1下部所设的抵块7上,考虑到结构的稳固性,抵块7与顶升板1焊接成一体,抵块7的作用是为了实现固定板2对顶升板1的直接驱动,减小力的传递过程中的损耗。考虑到固定板2驱动顶升板1的过程中,为了避免固定板2对振动电机3产生影响,振动电机3的最下端点高于抵块7的抵接面。
具体的,本实施例中设有两个油缸11和四组弹力组件5,两个油缸11到A通孔4的距离相等,四组弹力组件5到A通孔4的距离相等,即本实施例中,四组弹力组件5位于固定板2的四个边角的位置,两个油缸11的驱动杆与固定板2的两条宽度边的中部固定连接。
实施例10:
本实施例是在上述实施例9的基础上进行优化限定。
如图3-图5所示,夹紧装置包括卡瓦19和卡瓦座18。卡瓦座18固定在顶升板1的中部,卡瓦座18的轴线与安装孔的轴线一致,卡瓦19设于卡瓦座18内且该卡瓦19与自下向上依次穿过B通孔、A通孔4、安装孔、卡瓦座18的套管20抱紧,A通孔4、B通孔、安装孔、卡瓦座18的孔径均大于套管20的外径。
值得说明的是,本发明中的油缸11为两个时,则两个油缸11对称设于套管20的两侧,能够保证对起拔力的平衡,避免出现起拔歪斜,套管20卡死。
值得说明的是,A通孔4、B通孔的孔径均大于套管20的外径,套管20颤振幅度能够受控制,同时由于A通孔4、B通孔的孔径较大,在套管20颤振过程中,对油缸11底座和固定板2的影响较小,一定程度上也减小了对油缸11的振动。
当油缸11为两个,弹力组件5设置为两组时,油缸11和弹力组件5交叉间隔设置,即两个油缸11的轴线所在的平面与两组弹力组件5的轴线所在的平面相互垂直。
若油缸11为三个,弹力组件5为三组时,油缸11和弹力组件5交叉间隔设置。
若油缸11为两个,弹力组件5为四组时,各油缸11到A通孔4的距离相等,各弹力组件5到A通孔4的距离相等。
实施例10:
如图1-图5所示,本发明还提供一种采用上述振动结构的新型振动式液压拔管机,包括振动结构、驱动机构和夹紧装置,振动结构包括顶升板1、固定板2、弹簧杆5.1、振动弹簧5.2和限位件9,顶升板1与固定板2均为矩形且相互平行设置,顶升板1和固定板2所在的平面均与套管20的轴线相互垂直,顶升板1的下表面设有抵块7,考虑到结构的稳固性,抵块7与顶升板1焊接成一体,抵块7沿着顶升板1的长度方向对称设有两块,振动电机3为两个且分别安装在抵块7的侧壁上,考虑到固定板2驱动顶升板1的过程中,为了避免固定板2对振动电机3产生影响,振动电机3的最下端点高于抵块7的抵接面;弹簧杆5.1为四根,且该四根弹簧杆5.1分别设置在顶升板1与固定板2的四个边角之间,弹簧杆5.1的上端通过螺帽与顶升板1固定连接,振动弹簧5.2套设在位于顶升板1和固定板2之间的弹簧杆5.1上,振动弹簧5.2的上端与顶升板1相抵,振动弹簧5.2的下端与固定板2相抵,弹簧杆5.1的下端穿过固定板2上对应位置所设的A过孔,且该弹簧杆5.1伸出A过孔的一端套设有预紧弹簧8,A过孔的孔径大于弹簧杆5.1的外径,且该过孔的孔径小于振动弹簧5.2、预紧弹簧8的外径,预紧弹簧8的上端与固定板2的下表面相抵,预紧弹簧8的下端与设于弹簧杆5.1下端的限位件9相抵,位于固定板2长度方向上的两根弹簧杆5.1的下端所设的限位件9为一块共用的条形板6,条形板6的两端设有过孔B,弹簧杆5.1伸出A过孔的一端套设预紧弹簧8之后再穿过过孔B,该条形板6的两端通过限位螺帽10实现与弹簧杆5.1的连接。
为了方便对顶升板1进行搬运或吊起作业,顶升板1的两侧设有提手21。
驱动机构包括油缸11、油缸底座12、液压站13,油缸11为两个,油缸11设于油缸底座12上,油缸底座12上设有B通孔14,B通孔14与A通孔4的轴线一致,油缸11沿着B通孔14周向均匀设置,具体的,本实施例中为两个油缸11,两个油缸11对称设于套管20的两侧,能够保证对起拔力的平衡,避免出现起拔歪斜,套管20卡死,油缸11的驱动杆与固定板2固定连接,油缸11的进油管15与回油管16均与液压站13连接,进油管15与回油管16上设有液压换向阀17,液压站13通过电机带动油泵提供高压油液,高压油液经液压换向阀17后流入至油缸11内。
夹紧装置包括卡瓦座18和卡瓦19,卡瓦座18固定在顶升板1的中部,卡瓦座18的轴线与安装孔的轴线一致,卡瓦19设于卡瓦座18内且该卡瓦19与自下向上依次穿过B通孔14、A通孔4、安装孔、卡瓦座18的套管20抱紧,A通孔4、B通孔14、安装孔、卡瓦座18的孔径均大于套管20的外径。
由于条形板6位于固定板2长度方向的下方,因此,为了便于安装,油缸11与固定板2之间连接的位置位于固定板2宽度方向上的两组弹力组件5之间的中间位置。
A通孔4、B通孔14的孔径均大于套管20的外径,套管20颤振幅度能够受控制,同时由于A通孔4、B通孔14的孔径较大,在套管20颤振过程中,对油缸底座12和固定板2的影响较小,一定程度上也减小了对油缸11的振动。
此外,若采用油缸11为两个,弹力组件5、预紧组件也均为两组时,油缸11和弹力组件5交叉间隔设置,即两个油缸11的轴线所在的平面与两组弹力组件5的轴线所在的平面相互垂直。
值得说明的是,A通孔4、B通孔14的孔径均大于套管20的外径,套管20颤振幅度能够受控制,同时由于A通孔4、B通孔14的孔径较大,在套管20颤振过程中,对油缸11和固定板2的影响较小,一定程度上也减小了对油缸11的振动。
如图6所示,当固定板2上的驱动部2.1和振动调节部2.2均设置为两个,即油缸11为两个,弹力组件5和预紧组件均设置为两组,油缸11和弹力组件5交叉间隔设置,即两个油缸11的轴线所在的平面与两组弹力组件5的轴线所在的平面相互垂直。
若油缸11为三个,弹力组件5为三组时,油缸11和弹力组件5交叉间隔设置。
本发明还提供一种新型振动式液压拔管机的拔管方法,其中,包括如下步骤:
S1.安装套管20,将套管20依次穿过B通孔14、A通孔4、安装孔和卡瓦座18;
S2.安装卡瓦19,将卡瓦19安装在卡瓦座18内,并实现卡瓦19的卡紧面与套管20的管壁抱紧;
S3.拔出过程阶段一,操作液压站13上的控制阀,电机驱动油泵,进油管15输入液压油,油缸11的驱动杆上升,与驱动杆固定连接的固定板2上移,固定板2上移过程中振动弹簧5.2逐渐压缩,直至固定板2的上表面与设于顶升板1下部的抵块7相抵,振动弹簧5.2的压缩状态维持不变,驱动杆的继续上升,直接实现了固定板2对顶升板1的驱动,顶升板1上移的过程中,由于卡瓦19为上端厚度大于下端厚度的楔形结构,卡瓦座18上移对楔形结构的卡瓦19的挤压力逐渐增大,直至卡瓦19完全抱紧套管20,此后,驱动杆继续上升,向上的拉力便直接传递给套管20,套管20逐渐被拔出;
S4.拔出过程阶段二,当套管20与土体之间的摩擦力大于油缸11的驱动力时,油缸11的驱动杆便停止上升,此时振动电机3启动,动过振动电机3的振动,能够实现对套管20的颤振,套管20在颤振的过程中,防止套管20的卡死,能够一定程度的减小起拔力,振动电机3启动一定时间,油缸11驱动杆继续上升,再次对套管20拔出,该步骤可以重复进行;
S5.拔出过程阶段三,驱动杆继续上升到极限位置时,控制液压换向阀,油缸11驱动杆下降,固定板2随之下移过程中,固定板2与抵块7逐渐分离,振动弹簧5.2逐渐复位,之后驱动杆继续下移,预紧弹簧8逐渐压缩,预紧弹簧8对限位件9的推力直接通过弹簧杆5.1传递给顶升板1,实现弹簧杆5.1对顶升板1的下拉,弹簧杆5.1在下拉顶升板1的过程中,卡瓦座18对卡瓦19的夹紧力逐渐减小,直至卡瓦19松开,之后卡瓦座18继续下移,卡瓦座18与卡瓦19重新移动至起始起拔位置,重复上述操作。
本发明不局限于上述可选的实施方式,任何人在本发明的启示下都可得出其他各种形式的产品。上述具体实施方式不应理解成对本发明的保护范围的限制,本发明的保护范围应当以权利要求书中界定的为准,并且说明书可以用于解释权利要求书。