一种钻杆用螺旋截齿入岩钻头的制作方法
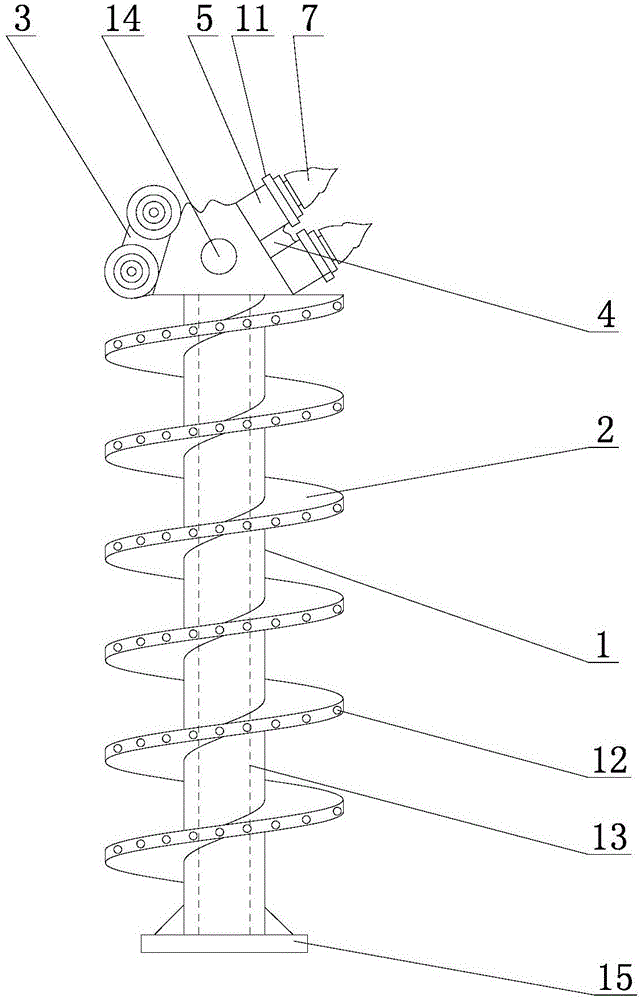
本实用新型涉及入岩钻头技术领域,尤其是一种钻杆用螺旋截齿入岩钻头。
背景技术:
钻头是工程机械中普遍用的的工具之一,在锚杆钻机中经常需要采用钻杆进行钻孔,正常情况下钻杆上都安装普通的钻头即可实现钻孔,但对于硬度较大的岩石层,要想进行钻孔则需要专门的入岩钻头。
目前,现有的入岩钻头一般采用牙轮式钻头进行入岩钻孔,但牙轮式钻头存在造价昂贵及钻孔速度低等不足,而且对高硬度的岩石层则无法进行钻进。
为了提高入岩钻孔效率,使入岩钻头设计更加合理,并趋于完善,现有技术进行了各种尝试,试图改善入岩钻头的性能,然而总是存在一些未尽如人意之处,例如中国实用新型专利CN2010202180326在双螺旋叶片和钻门上分别镶嵌截齿钻尖,实现钻进岩石层时,以点接触替代之前钻头的线接触或面接触,不仅提高了钻进效率,而且摩擦产热降低提高钻头寿命。但上述入岩钻头依然存在一些不足:一是截齿钻尖直接镶嵌在钻门和螺旋叶片上,当截齿钻尖因磨损损坏后导致整个钻头都无法继续使用,造成一定资源浪费,增加成本;二是截齿钻尖直接镶嵌导致截齿钻尖无法旋转,其磨损速度依然较快。因此,有必要对入岩钻头的结构进行优化,使其入岩钻孔性能进一步提高。
需要说明的是,上述内容属于发明人的技术认知范畴,并不必然构成现有技术。
技术实现要素:
本实用新型提供了一种钻杆用螺旋截齿入岩钻头,它具有结构设计更加合理、磨损小、截齿钻尖可更换、钻孔效率更高等优点,解决了现有技术中存在的问题。
本实用新型为解决上述技术问题所采用的技术方案是:
一种钻杆用螺旋截齿入岩钻头,包括钻头本体,所述钻头本体外侧壁上沿其轴线方向设有螺旋叶片,所述钻头本体下端对称间隔交错设有A组钻尖安装座和B组钻尖安装座两组钻尖安装座,每组钻尖安装座包括至少两个截齿钻尖安装支座,所述A组钻尖安装座和B组钻尖安装座上安装有相等个数的截齿钻尖安装支座,所述截齿钻尖安装支座上设有安装孔,所述安装孔内可拆卸连接有截齿钻尖且截齿钻尖相对安装孔旋转。
所述A组钻尖安装座和B组钻尖安装座倾斜设置,所述截齿钻尖轴线与钻头本体轴线夹角为40°-50°。
所述截齿钻尖轴线与钻头本体轴线夹角为45°。
所述截齿钻尖上转动安装有连接座,连接座与截齿钻尖通过轴承转动连接,所述截齿钻尖通过连接座可拆卸安装在安装孔内。
所述连接座上设有卡凸,所述安装孔内设有与卡凸配合卡接的卡槽,所述连接座与安装孔卡接连接。
所述截齿钻尖上现有限位垫片。
所述钻头本体外侧壁上沿轴线方向对称设有两组螺旋叶片,两组螺旋叶片侧壁上设有便于钻孔的半球形凸起。
所述钻头本体内设有注浆通道,所述钻头本体下端设有与注浆通道连通的出浆口。
所述钻头本体为圆管状结构。
所述钻头本体上端设有便于与钻杆连接的连接法兰。
本实用新型采用上述方案,针对现有入岩钻头存在的技术问题,设计了一种钻杆用螺旋截齿入岩钻头,通过在钻头本体上设计A组钻尖安装座和B组钻尖安装座,实现可拆卸安装截齿钻尖,同时将A组钻尖安装座和B组钻尖安装座的安装位置对称间隔错位设置,不仅可以方便的将磨损后的截齿钻尖进行更换,而且进一步提高钻孔效率;通过在截齿钻尖上转动设有连接座,在实现卡接的同时,截齿钻尖在工作时还可以旋转,进一步降低磨损,延长截齿钻尖的使用寿命。
附图说明
图1为本实用新型入岩钻头的结构示意图;
图2为本实用新型截齿钻尖安装支座的结构示意图;
图3为本实用新型截齿钻尖的结构示意图;
图中,1、钻头本体,2、螺旋叶片,3、A组钻尖安装座、4、B组钻尖安装座,5、截齿钻尖安装支座,6、安装孔,7、截齿钻尖,8、连接座,9、卡凸,10、卡槽,11、限位垫片,12、半球形凸起,13、注浆通道,14、出浆口,15、连接法兰。
具体实施方式
为能清楚说明本方案的技术特点,下面通过具体实施方式,并结合其附图,对本实用新型进行详细阐述。
在下面的描述中阐述了很多具体细节以便于充分理解本发明,但是,本发明还可以采用其他不同于在此描述的其他方式来实施,因此,本发明的保护范围并不受下面公开的具体实施例的限制。
另外,在本发明的描述中,需要理解的是,本发明中的“A组钻尖安装座”和“B组钻尖安装座”结构是相同的,主要区别在于安装的位置,目的就是降低磨损、提高钻孔效率;“连接座与安装孔卡接”是指卡接时连接强度能够满足钻孔的需求,但当需要更换截齿钻尖时可通过外力将截齿钻尖从安装孔内导出;另外需要理解的是本发明中的螺旋叶片、两组钻尖安装座镶嵌固定在钻头本体上的,不限定具体固定方式,例如焊接、一体铸造成型。
如图1-3所示,一种钻杆用螺旋截齿入岩钻头,包括钻头本体1,钻头本体1外侧壁上沿其轴线方向设有螺旋叶片2,钻头本体1下端对称间隔交错设有A组钻尖安装座3和B组钻尖安装座4两组钻尖安装座,每组钻尖安装座包括至少两个截齿钻尖安装支座5,A组钻尖安装座3和B组钻尖安装座4上安装有相等个数的截齿钻尖安装支座5,截齿钻尖安装支座5上设有安装孔6,安装孔6内可拆卸连接有截齿钻尖7且截齿钻尖7相对安装孔6旋转。通过在钻头本体1上设计A组钻尖安装座3和B组钻尖安装座4,实现可拆卸安装截齿钻尖7,同时将A组钻尖安装座3和B组钻尖安装座4的安装位置设置成对称间隔错位方式,不仅可以将磨损后的截齿钻尖7更换,而且进一步提高钻孔效率。
A组钻尖安装座3和B组钻尖安装座4倾斜设置,截齿钻尖7轴线与钻头本体1轴线夹角为40°-50°。受力更加均匀对称,运行更加平稳
截齿钻尖7轴线与钻头本体1轴线夹角为45°。夹角为45°时钻孔效率最佳。
截齿钻尖7上转动安装有连接座8,连接座8与截齿钻尖7通过轴承转动连接,截齿钻尖7通过连接座8可拆卸安装在安装孔6内。实现截齿钻尖7能够方便更换的同时使得截齿钻尖7在工作时可以旋转降低磨损,延长使用寿命。
连接座8上设有卡凸9,安装孔内设有与卡凸9配合实现卡接的卡槽10,连接座8与安装孔6卡接连接。卡接更加方便快捷。
截齿钻尖7上现有限位垫片11。
钻头本体1外侧壁上沿轴线方向对称设有两组螺旋叶片2,两组螺旋叶片2侧壁上设有便于钻孔的半球形凸起12。增大与岩石层的摩擦冲击,便于捣碎和导出岩石,钻孔效率进一步提高。
钻头本体1内设有注浆通道13,钻头本体1下端设有与注浆通道13连通的注浆口14。便于进行注浆,注浆更加方便。
钻头本体1为圆管状结构。
钻头本体1上端设有便于与钻杆连接的连接法兰15。便于安装在钻杆上。
本实用新型的工作过程:
使用时,通过连接法兰15与钻杆(中空钻杆,可实现注浆)连接,然后由锚杆钻机带动钻杆旋转钻孔,入岩钻孔时,截齿钻尖7对岩石层进行钻孔,钻孔时截齿钻尖7受摩擦力旋转,在提高入岩钻孔效率的同时有效降低截齿钻尖的磨损,当截齿钻尖7因磨损严重无法使用时,可将截齿钻尖7从安装孔6内导出,然后安装上新的截齿钻尖7。本申请的钻杆用螺旋截齿钻头具有结构设计更加合理、磨损小、截齿钻尖可更换、钻孔效率更高等优点
上述具体实施方式不能作为对本实用新型保护范围的限制,对于本技术领域的技术人员来说,对本实用新型实施方式所做出的任何替代改进或变换均落在本实用新型的保护范围内。
本实用新型未详述之处,均为本技术领域技术人员的公知技术。
- 上一篇:旋挖齿安装系统的制作方法
- 下一篇:一种抗震螺杆钻具的制作方法